The initial stage of PAT testing is the formal visual inspection; this formal visual inspection should only be carried out by a person competent to do so.
The results of the inspection must be documented
Conducting a Visual Inspection
When conducting the visual inspection the engineer must consider the following (basically they are doing a risk assessment at this stage):
Suitability of the equipment/environment: The equipment should be assessed for its suitability for the environment it is being used in, or the nature of the work being undertaken. When the work environment is harsh or hazardous particular care needs to be taken when selecting the equipment and assessing the frequency for PAT Testing.
Good Housekeeping: A check should be made to ensure the equipment is installed and is being operated in accordance with the manufacturers instructions and should:
- Locate the full length of cables
- Ensure there is a means of disconnection/isolation accessible
- Ensure there is adequate ventilation
- Ensure things such as cups and plants aren’t stored on appliances
- Ensure equipment is positioned correctly to avoid strain on the cables
- Check the equipment is being operated with the safety covers in place and any doors are closed
- Check that multi-way adaptors are being used correctly and extension leads aren’t being ‘daisy-chained’
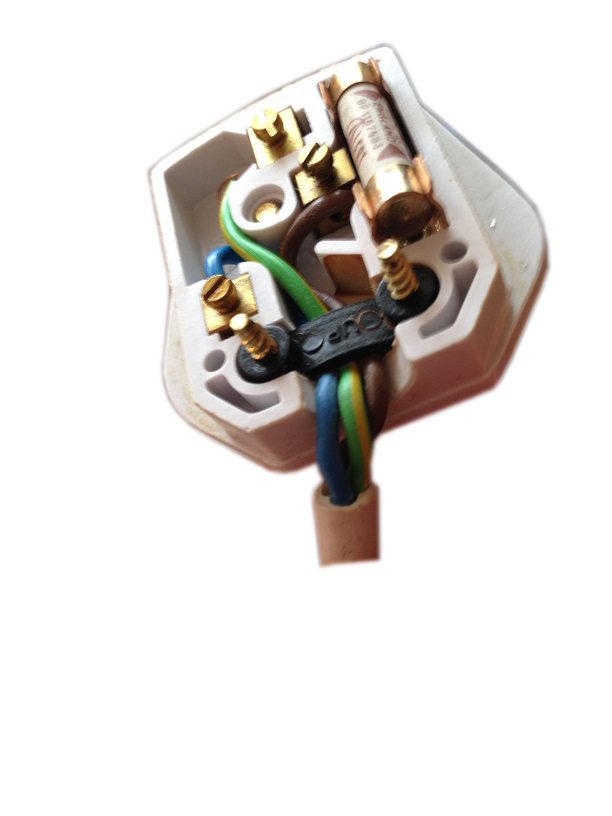
This plug would fail the visual inspection and need repairing – do you know why?
The condition of the equipment: The technician should check the appliance and lead:
- Check the full length of the flexible cable for damage
- Check the socket outlet
- Check the plug, including inside the plug
- Check the correct fuse is in place
- Check the appliance is not damaged in any way
- Check detachable power cords
- Identify any signs of overheating
- Check the plug top and cables are secure