What is PAT testing and why is it so important?
Portable Appliance Testing (PAT) is essential for ensuring your electrical equipment is safe and compliant. Whether you’re a business owner, landlord, tradesperson, school or office our expert PAT Testing service helps protect your staff and other users, helps you meet your legal requirements and keep your equipment in tip top condition.
All business owners or duty holders in a company are required by UK law, to ensure that all electrical equipment provided for use is safe to use at all times. To do this you need to put in place a system that checks and maintains the equipment, and keep a log of measures carried out.
You can do this in any way you like, but the easiest method is through PAT Testing. A thorough PAT service (not all companies provide what you need), will inspect and test your appliances, carry out maintenance as needed, and provide you with an itemised PAT Testing Certificate Report that includes electrical test results that show whether or not the appliance is safe.
If you have an accident at work and that accident is caused by faulty electrical equipment, e.g. a fire, electric shock, etc. then the accident investigators are going to want to see proof that the equipment was maintained and safe. If you can’t provide that, then you are in trouble.
If an electric heater catches fire, an extension lead overheats, a damaged cable gives someone a shock, and you are sued, you need to be able to prove you did everything possible to ensure the appliance was safe.
If you have risk assessments in place, and up to date PAT Testing Certificate reports showing those appliances, then you have some evidence that you have done everything you can to ensure that the equipment was safe. However, that evidence needs to back up that you have done everything – that means you have had the equipment checked recently enough to be considered an acceptable timeframe, and that users of equipment are encouraged to report new faults. Don’t think because it was PAT Tested 5 years ago, that that is enough.
Regular PAT testing; that is annual PAT testing, for most common workplaces is considered best practice and preferred by insurance companies. In some places testing should be carried out more often (such as building sites) and in others a less often frequency can be considered (e.g. offices with fixed equipment that never moves); but don’t try to decide that yourself – let us guide you; after all we are PAT testing experts! There is more information about PAT testing frequency here.
You must comply with the The Electricity At Work Regulations
The Electricity at Work Regulations (which is the guidance you should follow) require all workplaces to ensure electrical equipment provided for use at work (which also refers to home-workers and equipment in other business premises such as rental properties) is safe to use at all times, and requires you as the ‘duty holder’ of a ‘business’ to ensure that equipment maintains the required safety standards at all times.
How you do that is up to you, but the most recognised method, and generally the best option is what ‘we’ call PAT Testing. In full, Portable Appliance Testing which covers all electrical items fitted with a plug, is carried out to check and confirm that the item is safe, or to repair it, or remove it from safe, thus removing the risk of accident.
The electrical industry refers to the process as Electrical Equipment Testing (EET) because some appliances have been missed in the past, because business owners have ‘hard wired’ their appliances to the mains. This was done by an electrician, who took the plug off, and fed the flexible cable into a fused connection unit (white plate on the wall with a fuse and switch usually), hard wiring it to the mains wiring. Some of these items should only be checked by specialist engineers, but those that started life with a plug on should also be included in the PAT testing (although need someone competent to inspect them).
Inspection
We visually inspect every item for signs of damage or defects before testing. Catching issues early to ensure equipment is safe to use. We also make sure equipment is suitable for use.
Testing
We use industry leading calibrated PAT Testing equipment to check for earth continuity, insulation resistance and polarity; making sure each item meets the legal standards for electrical safety.
Repair
If we find any minor faults such as a broken plug or incorrect fuse, we carry out quick, free, on the spot repairs, to keep your appliances safe and compliant.
Report
You’ll receive a digital PAT testing Certificate listing all tested appliances, their location, the test results and any repairs carried out – perfect for your Safety records and compliance.
Comply
Our service ensures you meet Health and Safety regulations, insurance requirements, and duty of care responsibilities. With sensible guidance on retest frequency and reminders for retests.
About the PAT testing service we provide
The process of PAT testing is roughly the same for all equipment and all environments, whether you manage property, an office, school or factory we have to follow the same process when conducting our inspections. Here is an overview of that system:
Visual Inspection – each appliance is visually inspected including checking the plug, fuse and flexible cable. An appliance is any item of electrical equipment that is mains powered including cables, adaptors and the main unit. Battery operated equipment does not need PAT testing.
If a fault is found, the technician will repair it, or if not possible, the item will fail the inspection.
Repairs – Faults found require ‘remedial’ repair. These are repairs that affect the safety of the appliance and need to be done before the appliance can Pass. We do these for free; including repairing or replacing the plug, changing the fuse and repairing damaged cable.
We also assess the environment the appliance is being used in and its suitability.
Electrical Testing – Once the technician is happy that the appliance is visually safe testing commences. Tests using a PAT testing machine, are carried out to check internal safety, what the human eye can’t see. Is it wired correctly inside, are the internal wires damaged, is insulation in tact, etc. Not all appliances require these tests; for some the visual inspection is sufficient.
If the appliance passes the tests, it will be recorded on the technicians log. We record the appliance description, its location and the test results carried out. We record the electrical test reading acquired (not all PAT testers provide you with this, but it is essential if you’re ever investigated after an accident), and reference any repairs carried out.
The item is designated an ID number, which is cross referenced between the log and the label which we stick onto the appliance. Our labels are made in our office, branded and bespoke. They are attached to the appliance in a neat and tidy manner. We do our best to remove old labels first.
A failed appliance is labelled clearly with 2 Fail labels – one which details the fault, and another which we put on the plug for good measure. We also remove the fuse so if the item is accidentally plugged in, it won’t power on. It is reported to the site contact, and detailed in the report.
On completion of the inspection and testing, our technician will update the on site contact of their findings. This is useful stuff and will help you maintain a safe working environment. The technician will talk to you about retest periods, or may recommended further actions.
They will also ask you to review our work. Chances are you found us from our reviews or Google listings, and a review from you will help future clients too.
PAT Testing Certificate Report – The technician submits their data to the office to be compiled in a report. That report is created as a PDF document and sent to you attached to an email. For existing clients with good payment history, this is sent as soon as it is ready. For new clients we insist on payment first before sending the report; sorry but we have to do this to protect our selves. If you need the report urgently, pay quicker 🙂 We can do same day reports on advanced request.
Retest Reminders for Compliance – Once this job is done, and we have agreed a suitable PAT Testing frequency, we will put you in our system for next time, a date X months from now, depending on how frequent your testing will take place. This means you don’t have to remember when your PAT Testing is due. When the renewal date is approaching, about 8 weeks in advance, we will contact you to remind you we are coming on the anniversary of the inspection. If that date is not convenient we can change it.
That is an overview of our full process, from start to finish. It ensures you get the best possible service every time, and helps you to keep your business compliant.

We have been lucky enough to work with some amazing people and companies. We work primarily in office environments, and for local businesses. Whilst we have a ‘no job is too small’ philosophy, some jobs are too big – we tend not to take on jobs that have tens of thousands of appliances in one place, as it just takes far too long to do the job and these places drive the price down too much.
We enjoy working with local businesses, like coffee shops, salons, beauty parlours, office based businesses like accountants, legal firms and recruitment agencies. We work in doctors and dental surgeries, for landlords and letting agents testing in domestic properties, student lets and holiday homes. We work with other tradespeople, contractors and field engineers; we work in schools in the holidays, at nurseries and in care homes; hotels and so many more places; we’ll be here all day trying to list them all.
Rest assured we can help, if you’re not sure what’s involved, what you need or have questions give us a call, we could even book in a site visit before the testing appointment takes place.
At DRA PAT Testing, we don’t just check appliances are safe, we set the standard for it.
✅ We’ve been in the industry long enough to know what works – we know how best to service your needs, and ensure a swift, efficient service with minimal fuss. Our knowledge, professionalism and attention to detail means the job is done right the first time, every time.
✅ Over 500 verified 5-star reviews (396 on Google) – our clients don’t just recommend us, the rave about us. With hundreds of top rated reviews, our reputation is built on trust, reliability and exceptional service.
✅ Fast, flexible and hassle free – whilst others keep you waiting, we keep things moving. We work around your schedule, show up on time to set appointments, and deliver digital reports fast – often the same day.
✅ Fully qualified, insured and accredited technicians – all our technicians are fully trained, certified, insured and DBS checked, so you can feel confident that you’re in safe hands.
✅ We genuinely care about your safety – we’re not sticker jockey’s or box tickers; we treat every job as if we were testing equipment in our own business – because we take your safety seriously.
We combine expert knowledge, unbeatable customer service, and total reliability – that’s why more people choose DRA PAT Testing over anyone else.
Equipment included in the PAT testing process
Every part of the appliance is checked – All mains powered detachable, individual parts of the appliance need checking. Basically, if you unplug it and it stops working, then it is electrical equipment, and for purposes of danger prevention, it needs to be checked. This includes the mains wire (cable), any power switching devices (usually little black rectangular boxes attached to the cable), and the unit itself. Each of these is counted as an ‘item’ of electrical equipment. Each is inspected, and where necessary, tested. Each is labelled and recorded for the report.
Extension Leads – all extension leads, cable reels, etc that supply power are included in our inspections. The full length of the cable will be checked and any damage repaired.
Fixed Appliances – We carry out our inspections and tests on all types of electrical equipment that was intended by the manufacturer to have a plug – this includes any items that now don’t have a plug. These are called fixed appliances.
Fixed appliances have had the plug removed and the cable hard wired to the mains. This generally includes water boilers, heaters on walls, some televisions, hair dryers in hotels, etc. We also include integrated kitchen appliances where the plug can’t be accessed. Appliances that were never intended to have a plug, are not included – these generally are the ones you have service plans for.
A full inspection of the appliance, involves removing the cable from the mains, which should only be done by a competent person or electrician; we can do this, not all PAT testers can. We don’t do a full inspection as standard, because the power needs turning off, but it can be arranged. For more information see our fixed appliance testing page.
When we come across fixed appliances, whilst checking those with plugs, we do the best inspection we can. This always involves a visual inspection and in the case of ‘class 1’ appliances, we will conduct an earth continuity test between the socket circuit and the appliance.
Microwave Emissions Tests – Microwave ovens are slightly different to most other electrical appliances, in that as well as being powered on when plugging in, and providing an electrical safety risk, they also emit micro-wave radiation, which is an added risk that needs to be checked. So we check the door lock function works correctly, that there is not too much internal rust build up and that the micro-waves do not leak out of the door seal too much. More information is available on our microwave emissions page.
Equipment with Commando Plugs – commando plugs are the ones that look different to normal plugs – they are usually coloured yellow, blue or red, and are intended for use on building sites or where 230v would be considered too great a risk, so 110v (yellow) systems are used.
Blue 230v adaptors are used for equipment that needs higher protection than a 13amp fuse, such as for some commercial kitchen appliances and in factories, and in environments where higher voltage or 3-phase electricity is used we have red 415v plugs. These all have to be inspected as part of the PAT test.
Please note, these are not standard, and so command higher charges for the inspection and test, and may incur charges for repairs, however, we always check with you before doing chargeable repairs.
Server Systems – everyone is terrified that their server won’t turn back on; we never turn them off. If you want to, that’s up to you, but we don’t. We will do the best inspection we can, visually, of every part, and where possible do a check with a thermal image camera (they’re expensive, not all our engineers carry them). This means your server is included in the equipment log, but as it has not been unplugged we can’t check the plug meets the standards, so we recommend a full shutdown be arranged, at least once every 5 years. More information on Server System PAT testing.
What you get from PAT Testing
As well as peace of mind that your electrical equipment is safe, you also get a document that acts as evidence that you have done your duty to ensure your electrical equipment is safe; that is called the PAT Testing Certificate. It is a report that references the inspections carried out, and the results obtained.
Minimum industry standards require the report to include confirmation the appliance has passed, so a report with ‘Pass’ on it, is sufficient. The report will list the appliance, the test date, the engineer and that it passed.
However, a minimum standard report will not protect you in a legal dispute. For that you need real results that have meaning, so you need what we provide as standard (most PAT companies do not provide this):
- Electrical test readings for every appliance tested, that clearly show that the reading achieved is within the parameters of acceptable readings in British Standards; and where not, reasons given why.
- What repairs were carried out and what parts were supplied
- Why failed appliances failed their inspections and recommended actions.
With these 3 items on the report, you are much better protected.
When we test an appliance we record the test results and show them on the report (unless you tell us not to), if we carry out a repair we record it on the report – that’s an essential maintenance log of preventative maintenance.
About our PAT Testing Service
Our engineers are highly trained, qualified and competent to inspect and test electrical equipment. We also have passed DBS checks. Staff undergo regular Health and Safety training and hold CSCS cards.
All items are tested in accordance with the latest British Standards, PATTA and IET guidance.
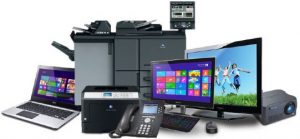
- Regular tests help you maintain safe electrical equipment
- The engineer assesses the suitability of an appliance for the environment it is being used in to help you comply with The Provision and Use of Work Equipment Regulations 1998
- PAT testing records can be used to demonstrate compliance with the Electricity at Work Regulations 1989
- Regular PAT testing helps you to comply with The Workplace (Health, Safety and Welfare) Regulations 1992
- Regular PAT tests in rental property help you comply with The Housing Act 2004 (England and Wales)
- PAT tests before the start of a tenancy help a landlord comply with The Ministry of Housing, Communities and Local Government’s guidance
- Regular PAT tests help you comply with The Electrical Equipment (Safety) Regulations 2016
- PAT testing finds plugs that don’t meet the Plugs and sockets etc. (Safety) Regulations 1994 and corrects it.
There are 10,000% more counterfeit electrical goods in the UK now than 20 years ago
Our engineers are fully aware of counterfeit goods and we’re always updating our knowledge of them, so if you them, we can spot them. Counterfeit electrical appliances, such as fake Apple chargers, or the fake ‘Lenovo’ laptop charger in these photos, are a major fire risk and have been proven to be the source of many domestic fires.
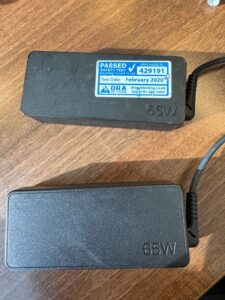
The top charger is genuine, the bottom is ‘fake’. Lenovo is a creditable brand in the IT industry producing some fine IT equipment, but buying a replacing laptop charger can be expensive, so people turn to online retailers for a cheaper option. This find, imported into the UK market is not a genuine Lenovo item, although through its embossed printing and design, is being passed off as such. This is an example of a counterfeit appliance.
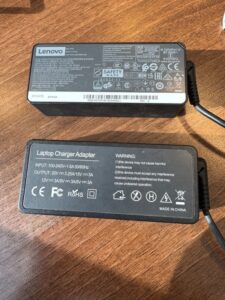